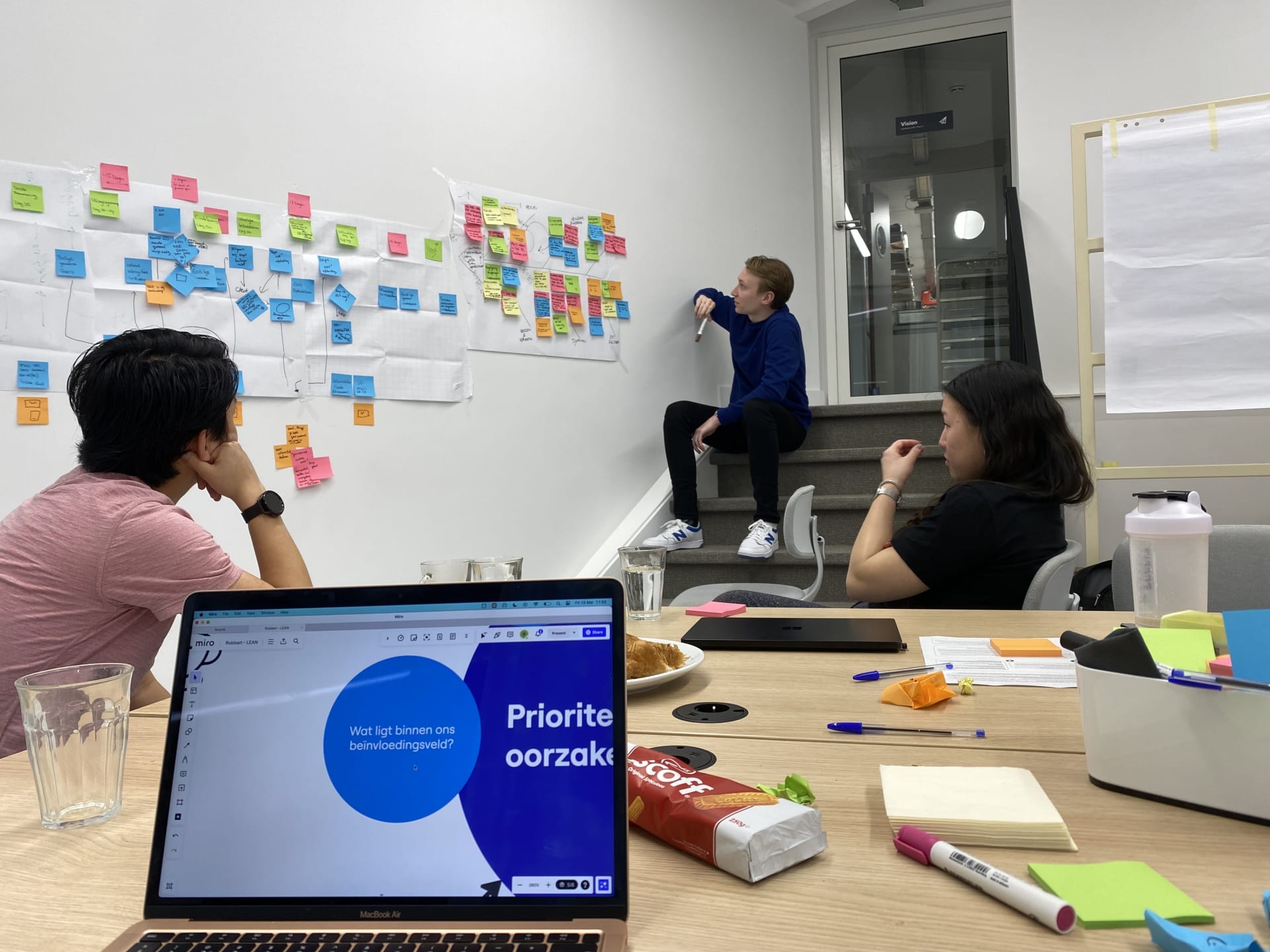
Brian, a Process Specialist at Vandebron, has initiated a LEAN project to reduce the number of errors in billing, focusing on "First Time Right" (FTR). LEAN is a methodology for process improvement that eliminates waste and increases efficiency. The necessity for this project arose from employee feedback about the complexity of billing and a low Customer Satisfaction Score (NPS). The goal is to become more efficient in handling customer inquiries about billing, which often takes a lot of time. Brian has completed the LEAN Green Belt training at Vandebron and facilitates the project team without in-depth knowledge of the subject: “I focus on improving processes and maintaining the right atmosphere during meetings. The project primarily focuses on problem analysis to understand the root causes of problems before proposing solutions.”
The project has faced challenges, such as balancing the sponsor's expectations (100% FTR) with realistic goals from the project team. The expected impact of the project is an increase from 60% to 70% First-Time-Right cases in billing, measured by weekly performance metrics.
Brian appreciates the collaboration and involvement of the project team, although facilitation is outside his comfort zone. He is proud of the proposed solutions, which are expected to bring significant improvement. Currently, the solutions are still in the implementation phase, but the initial signs are positive. He looks forward to further applications of LEAN within Vandebron and his own progress towards a LEAN Black Belt.
Also want to work on impactful projects? Check out our open positions.
Other projects
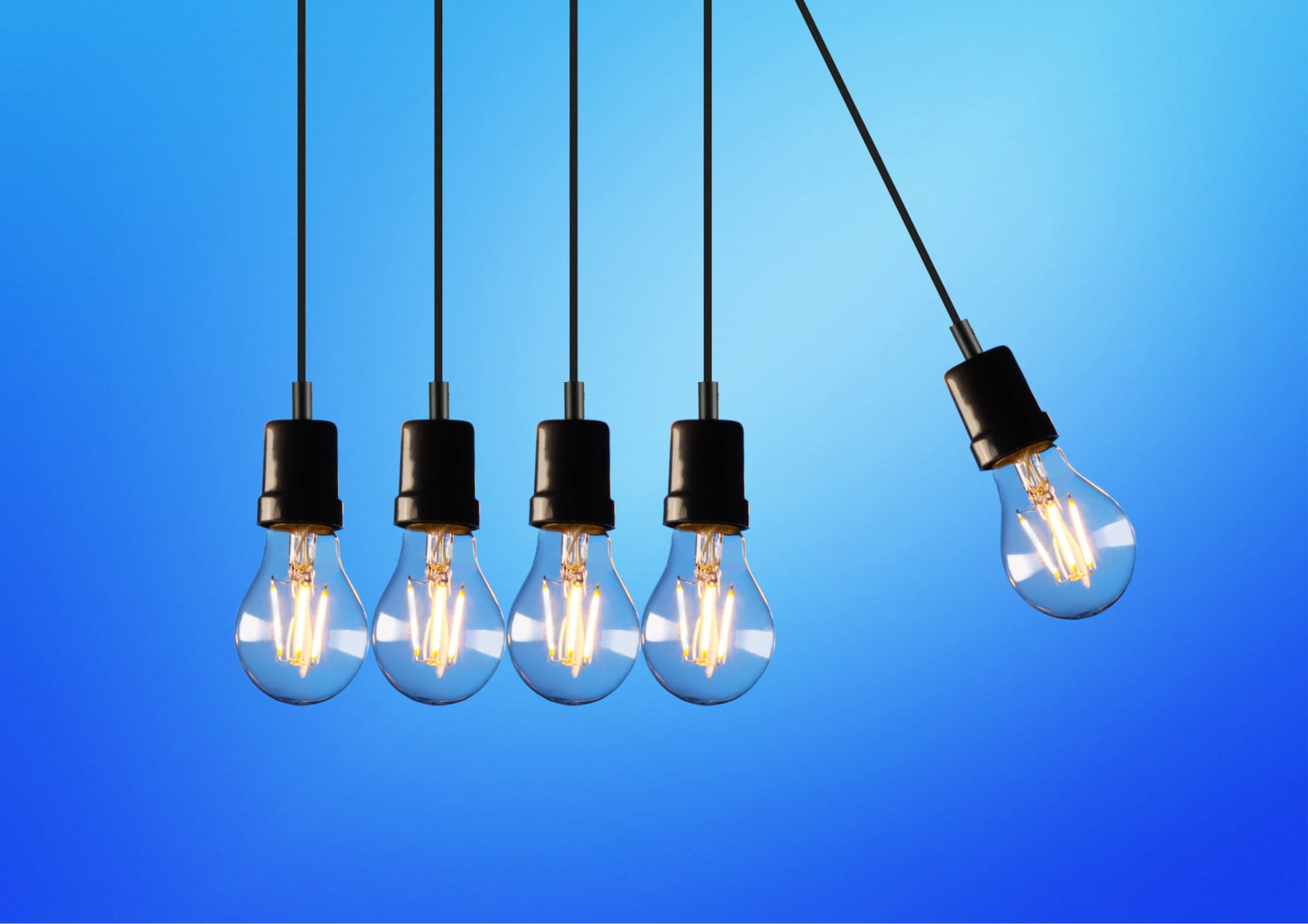
Dynamic contracts
Dynamic prices for energy. This motivates consumers to use energy at the greenest moment.
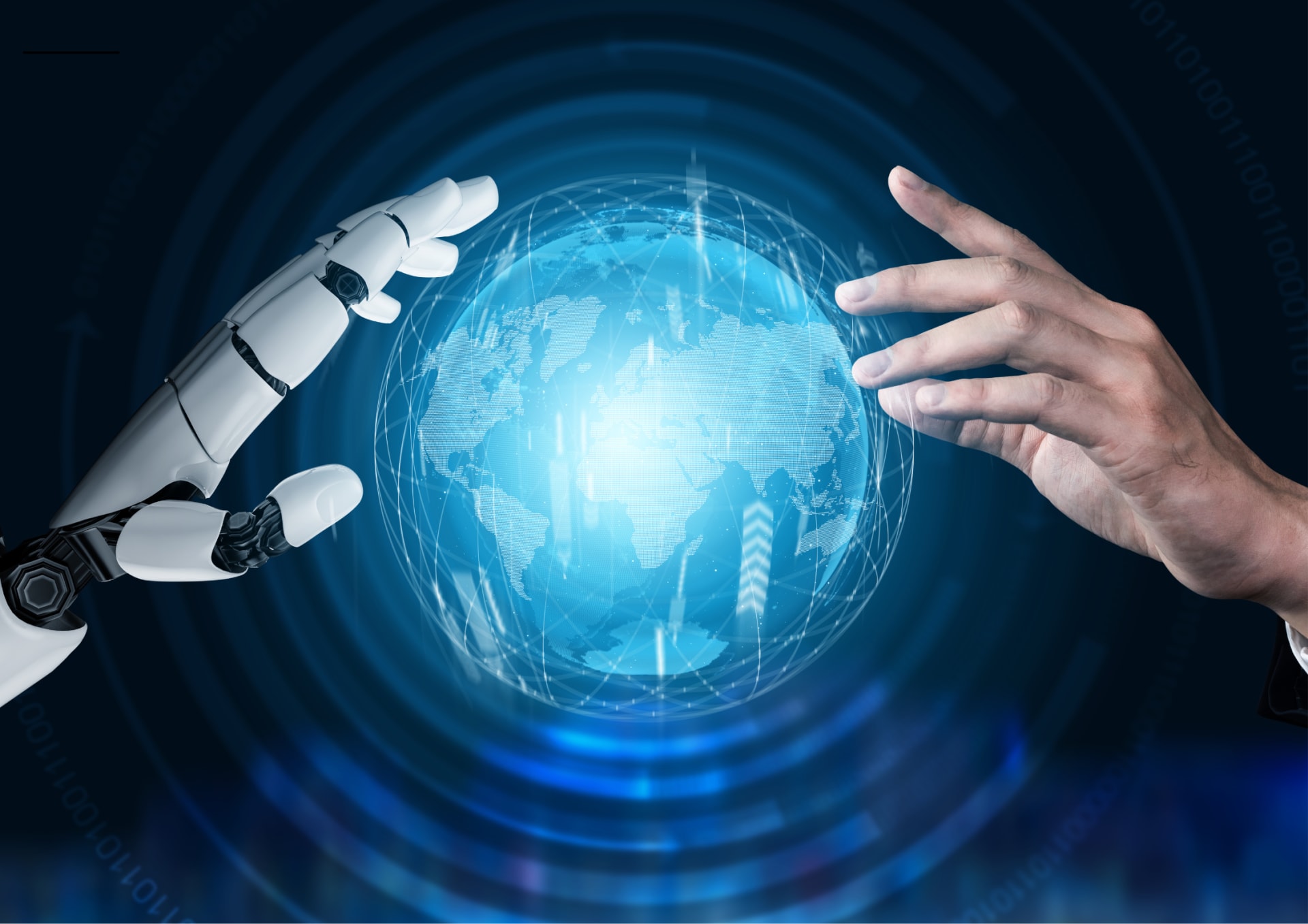
Implementing AI
How Bob works on implementing AI at our Customer Contact department.
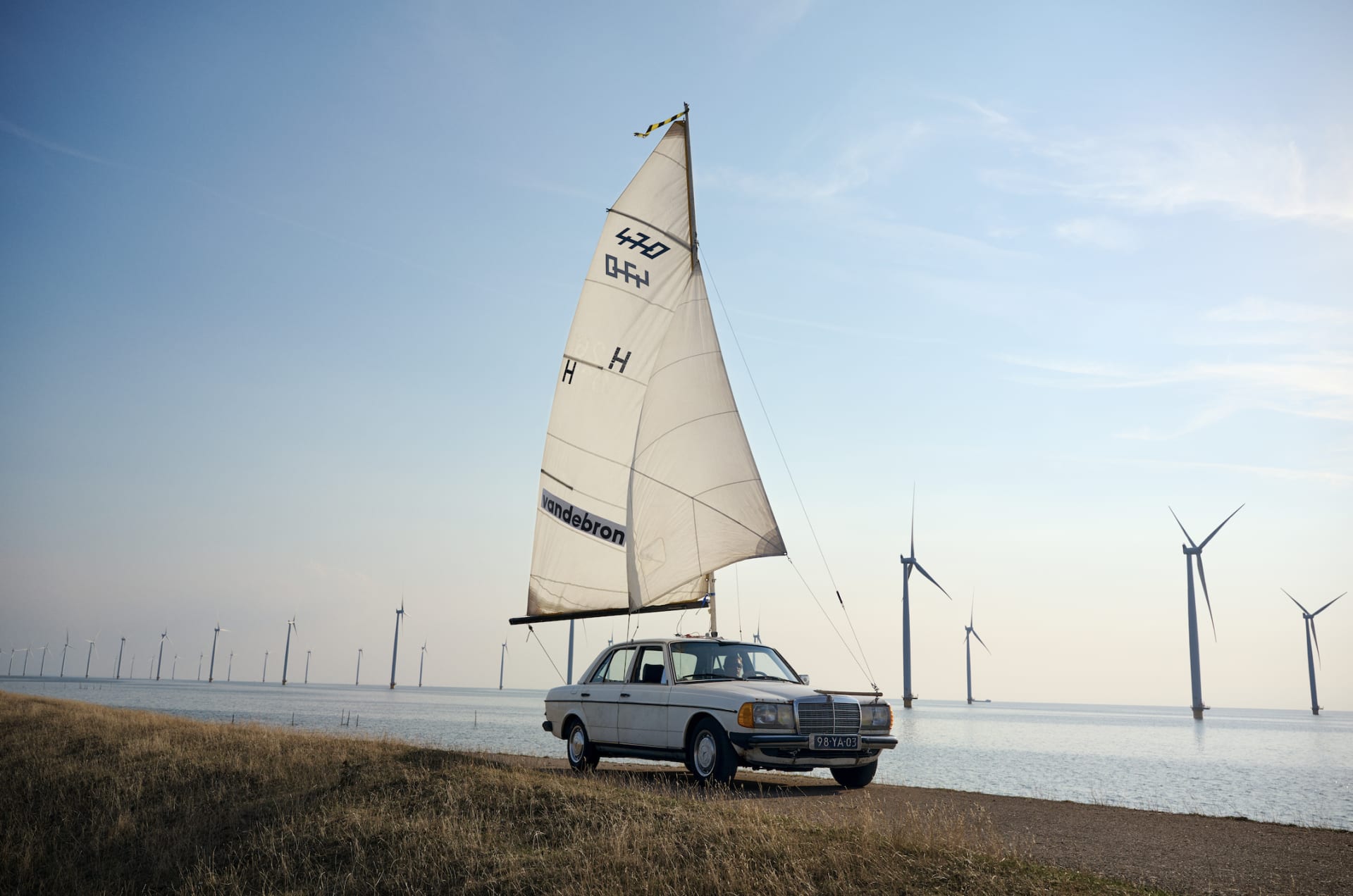
Smart charging collaboration
How we collaborated with electric vehicle company NIO to facilitate smart charging at a greater scale.